基于人工智能的智能制造微型产线
发布日期:2021-04-21 浏览次数:3442
概述
随着社会经济的发展,生产加工的特殊性、专业化、随机性对自动化生产线的生产效率、生产多用性、智能性以及灵活性提出了较高的要求。尤其是针对非固定节拍、随机供料等生产方式的自动化生产线,在正式投入使用的前期,需要对系统集成和控制方法进行大量的研究和调试工作。
智能化产线系统由机器人系统、传送带输送系统、视觉系统、气路系统、人机交互集中控制系统、智能环境支持系统构成。系统可完成工件的自动检测与位置信息的获取、工件的自动捡取和放置、载件盒在传送带上的循环输送、工件的自动卸载等操作过程,能够实现实际生产中工件捡取、加工过程的演示。
系统采用三条并联的不同传送方向的传送带及气缸推杆实现工件和包装盒的循环输送操作,采用工业视觉系统对工件进行图像信息以及位姿信息的获取;采用机器人及其抓手进行工件的捡取和装箱操作,采用滑台及其抓手对载件盒进行工件的卸载操作,通过对平台进行不同的设置实现不同的工作模式的运行。可对生产线上的不同工作模式的模拟和控制进行研究。
系统结构示意图
智能生产线系统模型
可通过对机器人搬运系统进行物理建模,以传送带走过一个工件长度所需的时间作为系统节拍,以机器人抓手空余量和工件分布信息作为状态,计算概率转移矩阵和性能矩阵,将机器人搬运生产线建立为DTMDP 模型。采用理论优化和仿真优化的方法,即通过策略迭代算法和基于模拟退火的Q学习算法对DTMDP模型求解。然后对策略迭代算法和Q习算法进行仿真和分析讨论,再根据仿真结果设置系统运行最优参数。
系统可以作为《现场总线及工业控制网络技术》、《智能生产计划管理》、《智能生产系统与cps建模》等课程的实践平台,结合大数据、深度学习和服务器系统,可以进行云制造,并将产线投入工业应用中,使得企业产线综合代价改进。
机器人搬运生产线工作流程
机器人搬运生产线系统模型
最优策略下系统行动示意图
主要组成部分
(1)人机交互集中控制系统
人机交互集中控制系统实现了操作者对实验平台的控制和实验平台的运行信息反馈显示。人机交互集中控制系统主要由服务器、PLC、触摸屏、按钮、指示灯、电表等组成。除服务器以外,人机交互系统集中设计于集中控制柜中。控制柜有两种工作模式,在调试模式下,可以通过控制柜面板上的按钮对生产线的某个设备进行手动调试或改变运行参数;在自动模式下,通过PLC 程序控制整个生产线自动运行。
作为系统的集成控制器,PLC 控制自动模式下的所有设备的上电、运行、运行停止和断电;PLC 接受来自光电传感器、按钮、电磁阀的数字输入(DI);通过数字输出(DO)控制继电器、电磁阀、真空发生器、指示灯等;通过脉冲输出控制传送带一、传送带二和十字滑台的伺服电机。服务器通过以太网实现视觉系统和机器人的通信,并实现对整个系统运行的组态监控;触摸屏通过 RS232 和 PLC通信,实现触摸屏对生产线的手动控制和运行状态监视。调试模式下,通过控制柜面板上的按钮,可以手动控制生产线的运行。
(2)实验平台监视系统
平台提供了 MelfaRXM.ocx 软件接口配合机器人自带的通信服务器实现的监控接口。MelfaRXM.ocx 控件是一个 ActiveX 通信控件,它支持连接多个机器人下位机控制器,也就是说,通过 MelfaRXM.ocx 可以通过机器人编号实现同时对多个机器人进行监控。对于单个执行监控程序的 PC 所能连接机器人数最大为 32,即机器人编号范围为 1-32。在使用 MelfaRXM.ocx 通信控件之前需要在程序加入通信控件,并在 Windows 注册表注册,经过正确的配置后,便可以在程序中使用 MelfaRXM.ocx 通信控件。
监控接口设计的主要原理基于请求响应机制,即通过发送特定请求给 RobCom服务器,等待服务器响应事件,捕获到响应事件后通过解码响应数据包获得相应监控数据。对于监视类请求,获得的响应为请求的响应数据;对于控制类请求,获得的响应为控制的结果即是否成功。
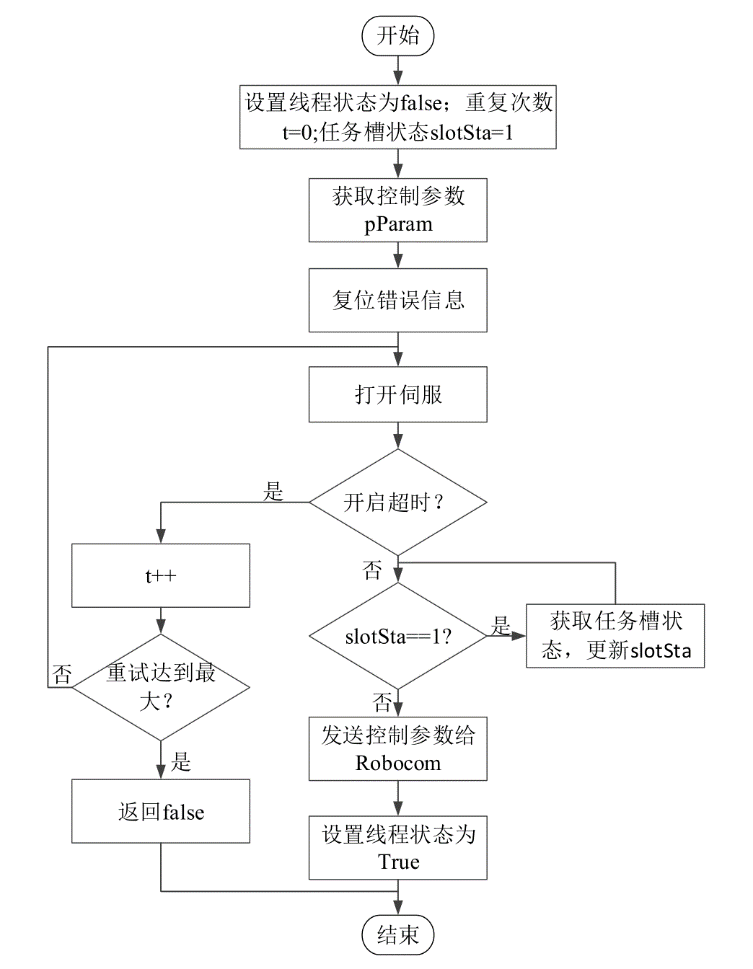
(3)最优化算法系统
机器人搬运系统优化目标是求一个最优调度策略,在平均或折扣准则下,长期运行下期望代价较低。但是在实际的生产系统中,还需要研究系统的一些其他性能指标,如工件流失率、单位时间内工件加工数量。
现实的生产加工系统中,工件到达率可能会发生变化,机器人的放置工件的时间也需要根据实际情况改变;工件到达率和机器人放置时间对生产系统的平均代价、生产效率、生产线率有很大的影响,因此研究不同工件到达率和机器人放置时间对系统性能的影响。
优化方法是先通过仿真或者观测实际系统的运行,得到一条或者多条样本轨道,通过采集到的样本轨道的信息来估计状态值函数,克服“维数灾”和“模型灾”问题,以对系统的性能进行优化。
根据实际机器人自动化生产线设置相关参数,其原则为使得生产线的到达率和机器人的平均生产率相平衡,以避免出现工件到达率过大导致的工件大量堵塞和流失,或者机器人移动速度过大导致的机器人发热和损耗。系统提供最优算法demo例程,可开发更多算法。